In the highly technical and efficiency-driven world of aerosol production, the completion of a turnkey installation is only the beginning. What follows is just as important—after-sales services, scheduled maintenance, technical support, spare parts management, and the continuous training of operational teams. In this essay, we will explore why these services are crucial, what they include, and how they can help maintain the operational efficiency of your aerosol filling line over time.
Why is Post-Aerosol Line Installation Support So Necessary?
For aerosol production systems to remain functional, safe, and efficient over the long term, post-aerosol line installation assistance is essential. Systems frequently need to be calibrated, tested for performance, and adjusted after installation in order to meet production needs and quality standards. Small problems like misaligned valves, irregular pressure, or automation errors can easily turn into expensive downtimes or safety risks if they are not properly supported.
Additionally, operational staff training, documentation updates, and system fine-tuning to meet the facility’s unique requirements are all included in post-installation support. Reliable assistance prolongs the equipment’s overall lifespan, guarantees that the line runs at maximum capacity, and upholds adherence to industry requirements.
To put it briefly, post-installation assistance is essential to maintaining operational excellence and optimizing return on investment, not merely a convenience.
What Do After-Sales Support Services Cover?
After-sales services for a filling machine are not limited to simple repairs. They are structured programs designed to ensure the seamless functioning of your aerosol line through its entire lifecycle. These services generally include:
- On-site and remote aerosol machine technical service
- Scheduled aerosol line maintenance visits
- Urgent machine troubleshooting and diagnostic interventions
- Access to certified filling machine spare parts
- Emergency response for system failures
Each support agreement can be tailored to the production load and criticality of your line. For instance, high-volume producers might benefit from more frequent inspections, whereas seasonal operations might require flexible service timelines.
In addition to technical assistance, turnkey installation after-sales support offers advice on how to maximize production, cut waste, and modify the line to meet new product requirements. This all-encompassing strategy keeps you competitive in a market that is constantly evolving.
What Types of Maintenance Should Be Performed for My Aerosol Filling Line?
Routine aerosol production line maintenance is the basis for equipment durability and production reliability. A thorough filling line maintenance agreement typically outlines three tiers of care:
- Preventive maintenance: routine inspections and repairs to guarantee that worn-out components are swapped out before they break. This entails lubricating moving parts, inspecting for leaks, cleaning valves, and confirming pressure systems.
- Predictive maintenance involves looking for trends that could point to a future problem using sensor analytics and performance data. System calibration is one of example of this.
- Corrective Maintenance: In reaction to malfunctions or breakdowns. This is where rapid aerosol machine support becomes crucial to minimize downtime.
How Can I Procure Spare Parts for My Aerosol Line?
The consistent availability of aerosol replacement parts is one of the most neglected yet crucial elements of efficient after-sales care. Working with a source who has original filling machine spare parts that match your machine’s model and setup is essential.
An whole production line can be stopped by delays in the acquisition of spare components. It is therefore advised to create a spare parts inventory plan as soon as possible following installation. Parts that are mission-critical and prone to rapid wear should be identified.
Certain turnkey suppliers provide parts kits or consignment stock that are especially tailored to the specifications of your equipment. This means that aerosol spare parts supply becomes integrated into your operational flow, reducing the administrative burden and procurement delays.
Can My Operators Receive Additional Training After Installation?
Yes, and they absolutely should. After the initial commissioning phase, your operators might still encounter challenges, especially if the line integrates complex automation, new product specifications, or advanced filling techniques.
After-sales services for filling machines often include post-installation training modules. These can be scheduled during maintenance visits or offered as remote sessions. They may cover topics such as:
- Operational best practices
- Safety protocols for pressurized systems
- Troubleshooting common alarms and errors
- Efficient changeovers for different product formats
Investing in the continuous education of your personnel ensures long-term autonomy, fewer operator errors, and improved productivity. An aerosol machine service that includes training keeps your team updated as the technology evolves.
How Can I Monitor the Performance of My Aerosol Line?
Numerous contemporary aerosol filling machines have networking features and digital interfaces. This enables managers and operators to keep an eye on data on component wear, downtime, error codes, and production speed in real time.
These data points can be transformed into useful insights with the help of a robust turnkey after-sales support system. Performance logs can be examined by service technicians to spot lags or irregularities. Predictive maintenance can be scheduled based on system alerts rather than on fixed dates.
Advanced aerosol line maintenance contracts occasionally incorporate remote diagnostics and monitoring software, which enables professionals to assess the functionality of your system in real time from off-site locations. This makes it possible to respond to problems more quickly and eliminates the need for in-person visits.
An continuing relationship between the equipment vendor and the user begins with the turnkey installation of an aerosol filling line. After-sales services for filling machines are the cornerstone of operational reliability and long-term value.
From scheduled aerosol line maintenance to rapid-response aerosol machine technical service, every layer of support adds to your production line’s resilience and adaptability. With access to certified filling machine spare parts, operator training, performance monitoring, and comprehensive machine troubleshooting, your investment remains protected and optimized.
By treating after-sales support as a strategic extension of your production capabilities, you’re not just maintaining machines—you’re maximizing their performance.
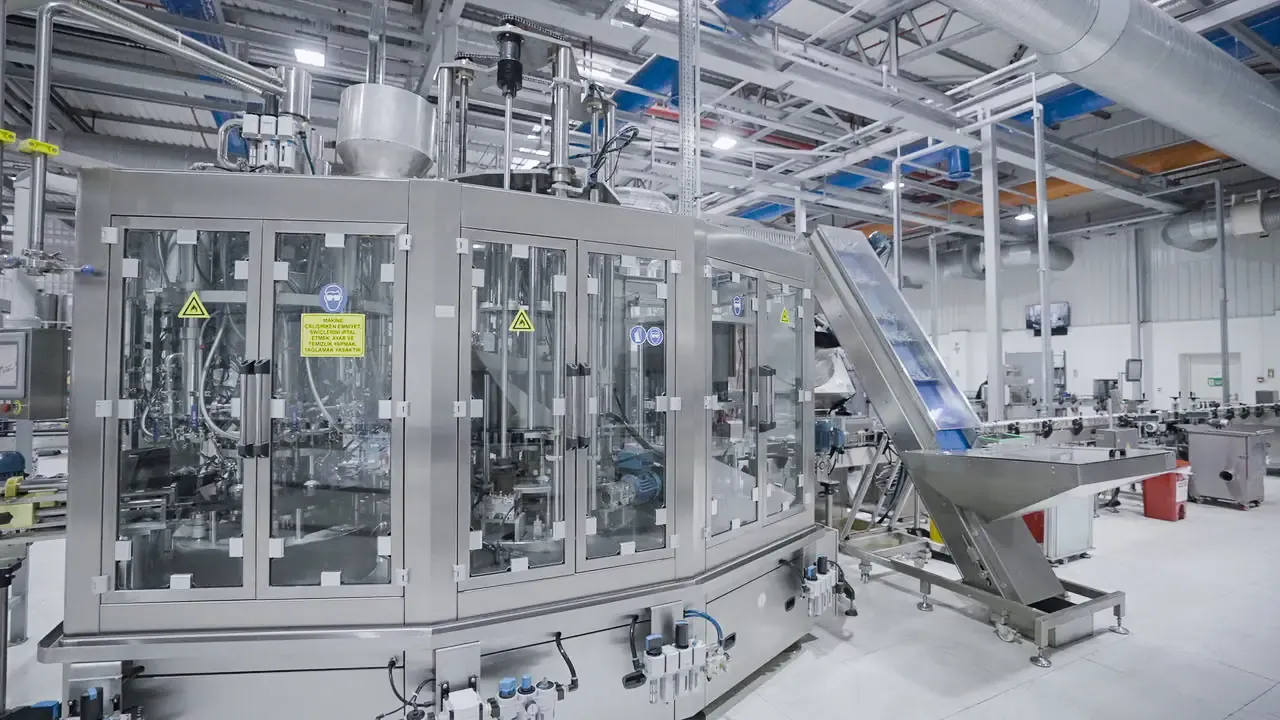