Safety is not only a part of the aerosol production sector; it is its foundation. Every step of the process requires following safety protocols when handling fast gear, flammable gases, and pressured materials. Regardless of the scale of the production—from a small batch to a huge industrial setup—it is imperative to have the right processes in place. Turnkey aerosol safety solutions can assist with that by offering comprehensive safety measures that give peace of mind, operational efficiency, and compliance assurance.
Why is Safety the Number One Priority in Aerosol Production?
Regarding industrial safety, one of the most vulnerable industries is the aerosol business. Error is impossible due to complex machinery, volatile substances, and pressurized systems. Serious mishaps or even explosions could be caused by a single spark, a small leak, or an alignment error during the filling operation.
Because of this, aerosol safety is a requirement rather than only a suggestion. Every component, from the design stage to the finished packaging, needs to meet strict requirements. Businesses that use aerosol filling machines are aware that safety is ingrained in the process and cannot be added on. Additionally, in this situation, selecting electrical components that are fire-proof and filling machines that are explosion-proof becomes a must rather than an option.
What Are the Main Risk Areas in Aerosol Production?
When evaluating the safety risks in aerosol production, several areas demand close attention:
- Filling Stations: One of the biggest danger zones. Pressure and accuracy collide here. Safety is essential while using aerosol filling machines because any overfilling, leaks, or poor sealing might cause risks.
- Crimping & Gassing Units: Infrastructure that is explosion-proof is necessary when handling combustible propellants. Dangerous consequences might arise from even the smallest mistake.
- Pressurized Storage Tanks: Flame arrestors, pressure release valves, and leak detection systems are required for handling and storing LPG, or other propellants.
- Electrical Equipment: Improper electrical setups can act as ignition sources. All systems need to be EX-proof, including motors, lighting, and control panels.
- Operator Interfaces: Human error remains a key concern. Operators must have proper training and should interact with systems that are intuitive and protected with automatic shutdowns.
Identifying these risk zones helps in designing industrial safety aerosol systems that mitigate risks at every level.
How Do Turnkey Aerosol Solutions Integrate Safety?
A turnkey aerosol solution takes the guesswork out of safety. It’s not just about delivering machines—it’s about delivering an entire ecosystem where safety is deeply embedded.
From the start, the layout design takes into account spacing, ventilation, and emergency exits. Explosion-proof filling machines, ATEX-certified components, flame detectors, and emergency stop systems are integrated during manufacturing—not added after the fact.
One of the biggest advantages of turnkey solutions is that safety comes standard, not as an optional upgrade. Turnkey aerosol safety solutions include:
- Pre-installed fire suppression systems
- Integrated gas leak sensors
- Centralized emergency controls
- Pressure monitoring and auto shut-off protocols
These systems are not only safer but smarter, often incorporating automation and IoT-based monitoring for predictive maintenance and early detection of anomalies.
Key Safety Features in Your Turnkey Line
When you invest in a fully integrated turnkey line, here’s what aerosol safety typically looks like:
- EX-Proof Components: Motors, control panels, junction boxes, and even lighting systems are explosion-proof and compliant with international ATEX standards.
- Automatic Leak Detection: Sensors placed across the line monitor gas levels and automatically trigger alarms or shut down the system if thresholds are crossed.
- Flame Arrestors & Gas Scrubbers: Designed to prevent flame propagation and ensure environmental safety.
- Overpressure Valves & Bursting Discs: Safety valves on storage tanks and filling lines protect against pressure spikes.
- Emergency Stop Systems: These enable prompt action through the strategic placement of buttons and centralized shut-off points.
- Fire Suppression Units: Systems that use dry chemicals or CO2 to quell fires, lowering damage and risk.
- Ventilation Systems: High-capacity exhausts guarantee air quality by eliminating flammable vapors.
Together, these components provide a comprehensive solution to aerosol filling machine safety that guarantees the security of the entire production environment.
Legal Compliance and Certifications: Registering Safety
Safety is a legal requirement as well as an internal policy issue. Turnkey aerosol solutions provide you with a smooth road through regulatory approvals because they are made to meet both local and international safety standards.
Common standards and certifications include:
- ATEX (Atmosphères Explosibles) for Europe
- IECEx certification for global explosion protection
- OSHA & NFPA for the US market
- CE Marking for European machinery directives
It is the duty of turnkey suppliers to guarantee that every component of the production line complies with regulations. This not only saves time but also reduces legal risks. With the documentation and certificates provided, your audits become smoother and your operation, more credible.
Supplier-Provided Safety Training and Operating Procedures
The best machinery is only as safe as the people operating it. That’s why supplier-provided safety training is a critical feature of a true turnkey solution. Reputable manufacturers don’t just deliver equipment—they deliver knowledge.
Operators are trained on-site or remotely on how to handle emergencies, operate machines safely, and follow standard operating procedures. Training programs often include:
- Start-up and shutdown protocols
- Emergency response drills
- Routine maintenance and inspection schedules
- Hazard recognition and mitigation
- Hands-on training with safety systems
In addition to training, clear operating manuals, signage, and maintenance documentation are provided. This creates a culture of safety across every level of operation and ensures your team is not only compliant—but confident.
Investing in Safety by Choosing a Turnkey Solution
Some companies view safety measures as an added cost. But in aerosol production, the cost of not investing in safety can be catastrophic. Turnkey solutions offer not only industrial safety aerosol systems but also long-term financial benefits.
By integrating safety from day one, you:
- Avoid costly retrofits and redesigns
- Prevent workplace accidents and downtime
- Enhance your brand’s reputation
- Pass audits and inspections with ease
- Gain trust from clients and regulatory bodies
Explosion proof filling machines, smart monitoring systems, and integrated SOPs reduce risks, improve efficiency, and protect both people and products. When you choose a turnkey line, you’re not just buying equipment—you’re buying safety, certainty, and sustainability.
In aerosol production, the question is not if safety should be prioritized—it’s how much safety can be built into the process. With turnkey aerosol safety solutions, the answer is: “as much as possible.” From design and compliance to training and execution, every element contributes to creating a secure, reliable, and efficient production environment.
In the end, safety is everything—and with the right turnkey partner, safety becomes effortless.
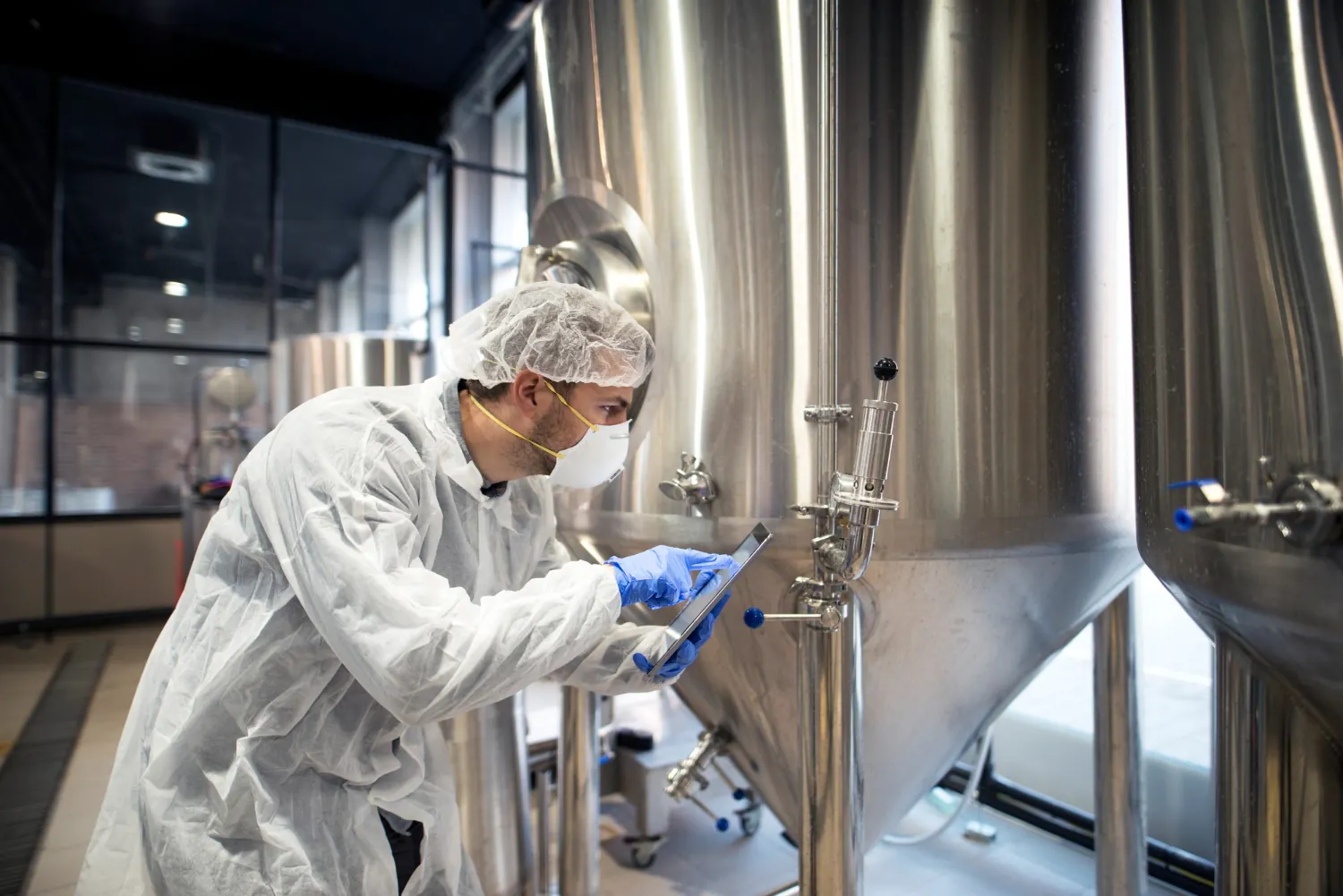