Aerosol packaging, though essential in many industries, is often associated with certain health and safety risks, especially for operators working on the production line. While aerosols are an essential part of our daily lives, from cleaning products to personal care items, their packaging involves the use of pressurized containers that require specific handling procedures. To ensure that aerosol packaging is performed safely, companies need to focus on improving ergonomics, reducing physical strain, and implementing safety protocols. This not only protects the workers but also ensures that the packaging process remains efficient and compliant with occupational health and safety standards. In this article, we will explore how to package aerosols while safeguarding operator safety, focusing on ergonomics, workstation design, the use of personal protective equipment (PPE), and accident prevention strategies.
Why is Ergonomics Important in Aerosol Packaging Operations?
Ergonomics plays a crucial role in the safety and efficiency of aerosol packaging operations. When operators work in an environment that is not ergonomically designed, they can experience discomfort, fatigue, or even long-term physical issues. Aerosol packaging ergonomics focuses on designing workstations, tools, and tasks that reduce strain and risk to operators.
Proper ergonomic practices can prevent repetitive stress injuries, musculoskeletal disorders, and other work-related health problems. For example, if operators must bend, stretch, or twist frequently while packaging aerosol cans, they may be at higher risk of back pain or joint issues. By addressing these ergonomic concerns, employers can ensure that workers remain healthy and productive.
Ergonomic workstation design also makes the packaging process more efficient. When tools and materials are positioned correctly, operators can perform tasks with minimal effort and maximum speed, reducing the likelihood of mistakes and improving overall productivity.
Which Manual Tasks Are Most Challenging For Operators?
Manual tasks in aerosol packaging that involve heavy lifting, repetitive motions, or awkward postures are often the most challenging for operators. These tasks can lead to muscle fatigue, joint strain, or even accidents if proper precautions are not taken. For example, lifting and positioning large, pressurized aerosol cans into boxes or onto pallets can strain the back and arms, particularly if the cans are too heavy or poorly positioned.
Similarly, tasks that involve repetitive motions, such as pressing buttons, sealing cans, or placing labels, can result in overuse injuries like carpal tunnel syndrome. Operators who have to reach for materials or twist their bodies to perform certain tasks are also at a higher risk of developing musculoskeletal disorders.
By identifying these manual tasks and addressing the ergonomic challenges they pose, companies can create safer work environments and improve the well-being of their workers.
How Does Ergonomic Workstation Design Affect Production Performance?
Ergonomic workstation design is essential for enhancing both operator safety and production performance. A well-designed workstation ensures that operators can perform their tasks comfortably and efficiently, which reduces fatigue and prevents injuries. This directly impacts the overall performance of the production line.
When workstations are designed with ergonomics in mind, operators can maintain a more natural and comfortable posture, which reduces the risk of strain or injury. For example, adjustable height workstations allow operators to adjust the setup according to their individual needs, minimizing the need for awkward movements.
Additionally, ergonomic workstations can help streamline the packaging process. When tools and materials are within easy reach, operators can work more quickly and with fewer errors, ultimately increasing the aerosol production line’s efficiency. This results in fewer downtime periods, improved workflow, and better overall output.
How Are Appropriate Height, Distance, And Position Determined For Operators?
Determining the appropriate height, distance, and position for operators in aerosol packaging lines is crucial for reducing physical strain and improving efficiency. Factors such as the size and weight of the cans, the type of task being performed, and the height of the operators must all be considered when designing workstations.
For example, workstations should be designed so that operators can reach materials without having to stretch or bend excessively. Ideally, the workstation should be at a height where operators can keep their arms at a natural, comfortable angle. This reduces strain on the shoulders, arms, and lower back.
The distance between the operator and the task should also be considered. If an operator has to lean forward constantly to reach materials, it can lead to fatigue and discomfort. Therefore, the task area should be positioned so that operators can reach it without straining.
In addition, adjustable equipment, such as height-adjustable tables or conveyor belts, can help accommodate different body types and tasks, ensuring that operators can work comfortably throughout their shift.
How Are Repetitive Motions Reduced in Aerosol Packaging Lines?
Repetitive motions, such as lifting, pressing, or placing cans, can be harmful to operators over time. To reduce the risk of repetitive stress injuries in aerosol packaging lines, companies can implement various strategies.
One effective method is to use automation and assistive devices. For example, conveyors can help transport aerosol cans from one station to the next, reducing the need for manual handling. Robots or automated machines can also be used to perform repetitive tasks like filling or sealing cans, which reduces the physical load on operators.
Another approach is job rotation. By rotating workers between different tasks, companies can ensure that no single operator is performing the same repetitive motions for extended periods. This helps to reduce strain on specific muscle groups and minimizes the risk of injury.
Finally, it’s essential to encourage regular breaks for operators to stretch and rest. This helps to alleviate tension in muscles and joints, reducing the risk of overuse injuries.
How Are Risks Such As Noise, Temperature, And Gas Leakage Controlled?
In aerosol packaging operations, various environmental factors, such as noise, temperature, and gas leakage, can pose significant risks to operator safety. These factors must be carefully managed to maintain a safe working environment.
Noise control is essential because prolonged exposure to high noise levels can cause hearing loss or other health issues. Companies should implement noise-reducing measures such as soundproofing, noise barriers, and hearing protection equipment like earplugs or earmuffs.
Temperature control is equally important. Aerosol cans are often sensitive to temperature fluctuations, which can cause pressure buildup or leakage. To protect operators, the work environment should be kept at a controlled temperature. This helps ensure that aerosol cans are stored and handled safely while also keeping the operators comfortable.
Gas leakage is another concern in aerosol packaging, especially since many aerosols contain flammable or toxic gases. To prevent leaks, companies should use proper sealing techniques, inspect cans for defects, and install ventilation systems to disperse any hazardous gases. In addition, gas detection systems can be installed to alert operators to any potential leaks.
What Role Do Emergency Stop Systems Play in Operator Safety?
Emergency stop systems play a critical role in operator safety by allowing workers to quickly halt the production line in the event of an emergency. These systems are essential for preventing accidents and protecting operators from potential hazards, such as equipment malfunctions, gas leaks, or fires.
In aerosol packaging lines, emergency stop systems should be easily accessible and clearly marked. Operators should be trained to use these systems effectively to minimize response time during emergencies. Additionally, regular drills and safety checks should be conducted to ensure that all emergency stop systems are functioning properly.
Is The Use of Personal Protective Equipment (PPE) Sufficient? Which Equipment is Essential?
While Personal Protective Equipment (PPE) is a critical part of safety in aerosol packaging, it is not the only solution to preventing workplace injuries. However, PPE serves as a final line of defense, protecting operators from hazards that cannot be eliminated through other means.
Essential PPE for aerosol packaging operations includes gloves, safety glasses, ear protection, and flame-resistant clothing. Gloves protect operators from sharp edges or hot surfaces, while safety glasses prevent eye injuries from flying debris or accidental splashes. Ear protection is necessary to shield workers from the high noise levels common in industrial environments. Flame-resistant clothing is crucial for operators working with flammable aerosol products.
While PPE is essential, it should be combined with other safety measures, such as ergonomic workstation design, proper training, and hazard control procedures, to ensure a comprehensive safety strategy.
How Are Training And Ergonomics Awareness Increased to Prevent Work Accidents?
To prevent work accidents in aerosol packaging operations, it is essential to provide thorough training for operators. Training programs should focus on ergonomics, proper lifting techniques, and the safe use of machinery and equipment. Operators should also be educated about the specific hazards associated with aerosol products and how to handle them safely.
Increasing awareness of ergonomics is crucial to ensuring that operators understand the importance of proper posture, workstation design, and task rotation. Companies can promote this awareness through workshops, demonstrations, and ongoing training.
Additionally, involving operators in the process of improving ergonomics can lead to better safety outcomes. Workers who are aware of ergonomic principles and feel comfortable suggesting improvements are more likely to follow safety protocols and identify potential hazards before they become problems.
How Are Production Speed And Quality Increased With Ergonomic Improvements?
Ergonomic improvements not only enhance operator safety but also lead to increased production speed and quality. When operators work in a comfortable, ergonomically designed environment, they can perform tasks more efficiently and with greater accuracy.
For example, reducing physical strain allows operators to maintain focus and energy throughout their shifts, leading to fewer errors and higher-quality products. Additionally, ergonomic workstations reduce fatigue, which in turn decreases the likelihood of mistakes or accidents that could slow down the production line.
By improving ergonomics, companies can achieve a balance between worker safety, efficiency, and product quality, resulting in a more productive and profitable operation.
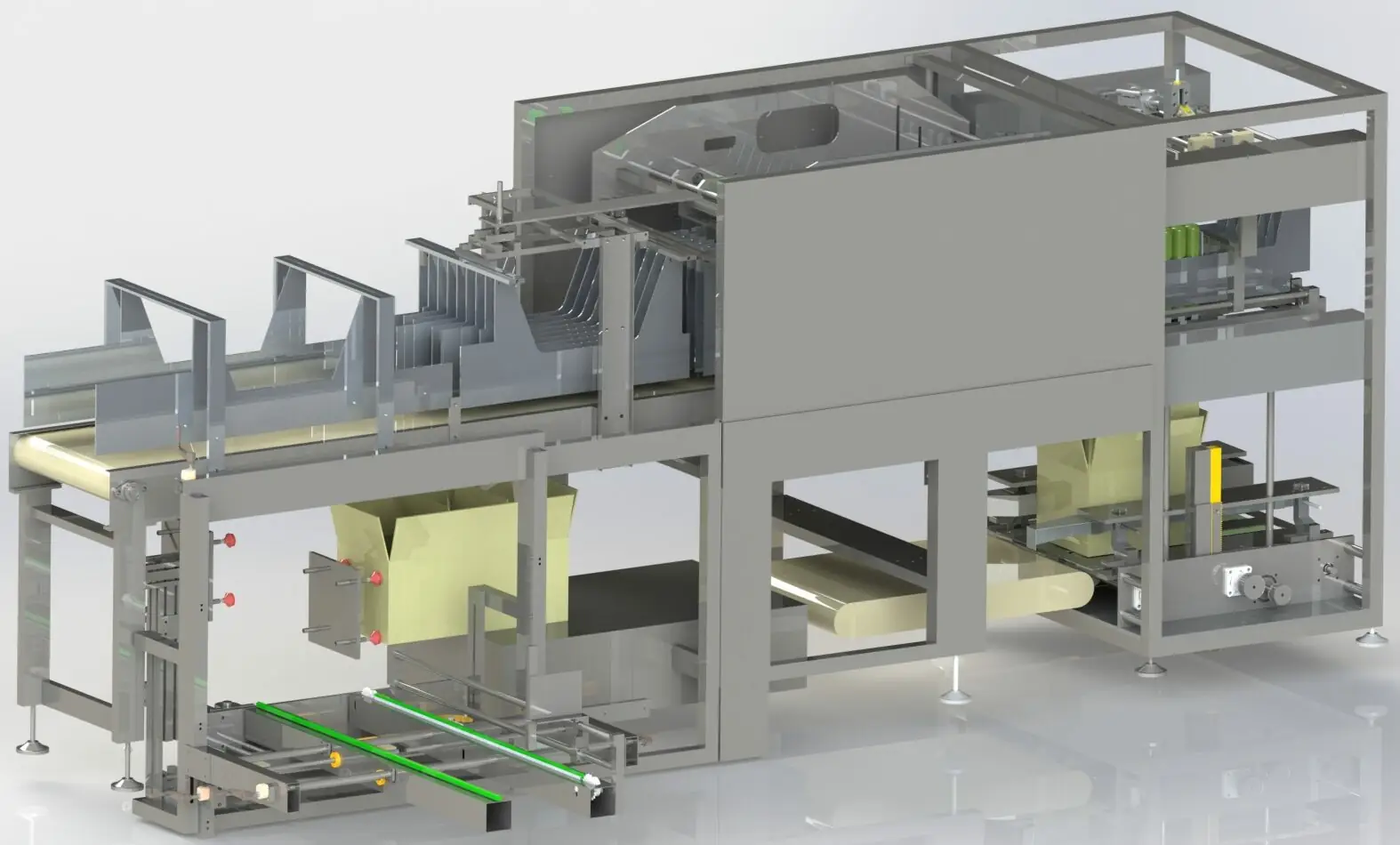