GENERAL
- Type : Standard Transportable Hydrocarbon Filling Room
- Construction : Container
- Rating : ATEX II 2G Compliant
- Sized for : Single Rotary/Indexing Machines
- Design Pressure :4,8 kn/m2 on all Four Insulated Walls
- Explosion Relief : Roof Area
- Roof : Fire retardant sheet PVC roofing cover and secured on the roof with fastening rope or chain
- Paint of structure: Flameproof and flame delayer
- Lighting : Explosion proof zone 2 fluorescent strip lighting
- Egress doors: 2 pcs on sides
- Windows: 2 laminated
- Windows for conveyor belts: 2 pcs or 1 pcs (depends on line lay-out)
- Fire fighting : One fire extinguishing ball is mounted inside the gas house
- Flame detector: 1 infrared (IR3)
- Gas detector: 2 pcs infrared (gas house) , 1 pcs infrared (gassing machine)
- UPS system in case electricity cuts
- One automatic and manual isolation at the outside of gas house (as close as possible), one manual isolation valve inside the gas house
- The pressure inside the gas house and gasser will be kept in negative pressure
PHYSICAL
- Width 3000 mm
- Length 3000 mm
- Height 2500 mm
VENTILATION
- The gas manager panel has a PLC panel containing the operator controls and indicators. A key switch is provided to enable the start and stop push buttons. This is used during the system start up and shutdown routines.
- Two independent extration fans (on gas house); one runs continuously
- One extration fan (on the gasser)
- One fresh air blower
- The fans are mounted externally on a fabricated steel platform. They are connected to the internal primary and secondary ventilation ducting through the gassing room wall, and to the external ducting. The fans are ex-proof and electrically controlled through the gas manager, and are connected to the gas manager.
- Ventilation ensures a minimum of 60 air changes per hour (normal) and a minimum of 120 air changes per hour (high)
- Flow sensors are installed and linked to the stop filling in case of loss of flow is detected
Primary ventilation system for gasser machine
- Fans : 2-Speed Explosion Proof Fan
- Rating : 2950 CFM [5000m3] at 1400 RPM,1475 CFM [2500 m3] at 700 RPM
- Motor : 2.2 Kw-380VAC-3ph-50Hz
Primary ventilation system for gas house
- Fans : 2-Speed Explosion Proof Fan
- Rating : 2950 CFM [8000m3/h] at 1400 RPM,1475 CFM [4000 m3/ h] at 700 RPM
- Motor : 2.2 Kw-380VAC-3ph-50Hz
Secondary ventilation system for gas house
- Fans : 2-Speed Explosion Proof Fan
- Rating : 2950 CFM [5000m3/h] at 1400 RPM,1475 CFM [2500 m3/ h] at 700 RPM
- Motor : 2.2 Kw-380VAC-3ph-50Hz
Fresh air blowing system
- Fans : 2-Speed Explosion Proof Fan
- Rating : 2950 CFM [4000m3] at 1400 RPM,1475 CFM [2000 m3] at 700 RPM
- Motor : 2.2 Kw-380VAC-3ph-50Hz
ROOF
- Fire retardant sheet PVC roofing cover and it is designed to prevent flying parts from escaping the confines of the gas house.
- The roof is secured to the gas house by elasticated roof fastening rope or chain
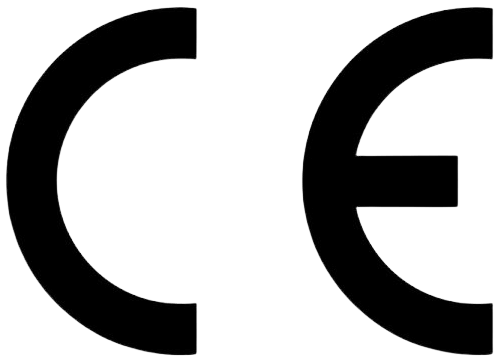
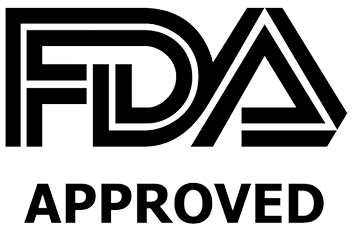
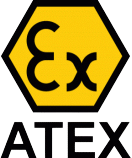
CCTV CAMERA AND MONITOR OPTION
- A color camera is mounted inside the gas house, above the large access door. This camera, when selected, is contained within an explosion proof enclosure, and monitors the gassing machine operation. An optional remote color monitor, located in a non-hazardous area, provides visualization of the gassing machine to operating personnel.
GAS DETECTION SYSTEM
- The gas sensors indicate the presence and level of gas and automatically initiate safety functions. Butane and propane mixtures with air are flammable within the explosive limits which are between approximately 1.8% to 10% v/v. The lower figure is called the lower explosive limit (LEL).