In the industry that produces aerosols, quality control is more than just a manufacturing process. It offers the structure for guaranteeing that every product manufactured at the plant is dependable, safe, and satisfies industry and customer standards. Every step of the production process, from the choice of raw materials to sophisticated automation technology, necessitates close monitoring and assessment. This essay explores the best practices and standards that lead to continuously good quality in the field of aerosol production.
Why is Quality Control So Important in Aerosol Production?
In the production of aerosols, quality control is about preventing errors before they occur, not only about identifying them. By definition, aerosol products contain pressured materials. Therefore, even a minor mistake could result in recalls, safety risks, or even customer injury. A strong quality management system, extensive inspection, and ongoing monitoring are therefore essential.
Cans leaking, broken valves, irregular spray patterns, and in severe situations, explosions, are all consequences of poor-quality control. This can result in monetary losses and legal problems in addition to eroding consumer trust. Because of this, manufacturers of aerosols must take a proactive approach to quality control. It must be incorporated into all stages of the procedure, not simply the final one.
Which Standards and Regulations Are Applied in Aerosol Production?
There are numerous local and international rules that businesses must abide by when producing aerosols.
In addition, a lot of businesses implement internal standards in response to client demands or outside certifications. These may involve stricter standards than those outlined in the legislation. In addition to keeping, you out of trouble, adhering to these rules demonstrates to your clients and partners your appreciation for quality.
It’s also important to remember that regulatory environments change frequently, so staying current is part of the challenge. It is like playing with fire for a small-batch enterprise or a multinational player to ignore standards.
How is Raw Material Quality Controlled in Aerosol Production?
The raw ingredients are where quality begins. You cannot expect good returns if your input is poor quality. Therefore, all of the parts that go into making aerosols, such as propellers, solvents, containers, valves, and even labeling materials, need to be properly chosen and assessed.
Manufacturers typically work with dependable suppliers and have strict quality standards for every delivery. Before a batch of raw materials is used in production, it is examined and sampled. Purity, moisture content, and pressure tolerance are among the details that are looked at. If raw material does not fulfill quality standards, a production line rarely stops completely.
The results could be affected by even minor changes to the ingredients. To guarantee raw material homogeneity, quality control teams typically collaborate closely with procurement. Like how you can’t use inexpensive ingredients and expect five-star outcomes when cooking a fantastic dinner.
What are the Effective Monitoring and Inspection Methods in the Aerosol Production Process?
Monitoring each stage becomes crucial once production starts. Inspection and monitoring are ongoing processes rather than one-time events. These consist of performance testing on the spray and discharge rates, weight checks, pressure tests, and visual inspections.
Inline inspection systems, which provide real-time quality assessments as items pass through the line, are used by certain businesses. By identifying flaws early on, this can reduce waste and boost productivity. At certain times, technicians and quality control staff also conduct thorough audits and spot checks.
Carefully recording inspection data results in a paper trail that can be utilized for improvement analysis or traceability. In other words, you will encounter fewer surprises later on if you have more eyes watching the process.
What are the Best Practices for Error Reduction and Process Improvement in Aerosol Production?
Designing errors out of the process from the start is the simplest way to handle them. This entails making training investments, establishing transparent protocols, and fostering an accountable culture. The significance of quality control should be understood by every employee on the production line.
Root cause analysis is another aspect of error reduction. Fixing something is not enough when it goes wrong. You need to figure out what caused it and how to keep it from happening again. This can entail modifying machine settings, training protocols, or even vendor swapping.
How are Advanced Technologies and Automation Systems Used for Quality Control?
Technology and automation are revolutionizing quality control. Machines never grow weary or miss anything. Automated systems in aerosol manufacturing can detect fill levels, test pressures, inspect can seem, and even reject defective goods without the need for human intervention.
For example, vision systems employ AI algorithms and high-resolution cameras to identify flaws instantly. These systems’ data can be rapidly examined and used to make real-time process adjustments. Better products, less waste, and fewer mistakes result from this.
Additionally, automation isn’t limited to inspection. It is employed in a variety of processes, including mixing, filling, packaging, and batching ingredients. Automation helps guarantee that every product satisfies the same exacting requirements by standardizing these procedures.
Naturally, technology only functions properly when it is calibrated and maintained. Therefore, routine system updates and checks are essential.
How Should Quality Control Results Be Reported and Monitored in Aerosol Production?
The only way to make data valuable is to use it. For this reason, monitoring and reporting are essential. Digital quality management systems (QMS) are used by the majority of aerosol manufacturers to document test results, inspection information, and deviations. Real-time reviews of dashboards and reports is possible with these solutions.
Frequently tracked KPIs include defect rates, downtime, and customer complaints. In the event that figures start to trend in the incorrect direction, alerts can be set off automatically. This makes it possible for quality teams to act swiftly before things get worse.
Additionally, reports are necessary for both internal and external audits. A strong reporting procedure makes it simple to provide the thorough, high-quality documentation that regulators and clients frequently need.
Team evaluations and regular quality meetings keep everyone on the same page. Quality isn’t a one-person job, after all. It’s a team sport.
What are the Continuity and Improvement Strategies for Quality Management in Aerosol Production?
Upholding high standards of quality takes time and effort. It’s a continuous endeavor. Aerosol producers therefore require effective continuity and improvement plans.
Training is the first step, all production staff should receive regular training on the latest standards, procedures, and technology. New personnel should be subject to a thorough onboarding process that prioritizes quality standards.
Second, companies need to create a culture that welcomes criticism. If someone sees a problem or has a change proposal, they should feel free to express their concerns. Openness like that results in quicker fixes and wiser choices.
Third, regular internal and external audits maintain process integrity and everyone’s honesty. You can clearly see where you stand when you compare yourself to industry leaders.
Finally, maintain your flexibility. Markets fluctuate. Rules change throughout time. New technologies and materials are developed. Businesses that remain inquisitive and flexible are the ones that prosper.
In conclusion, quality control in aerosol manufacturing entails more than simply checking boxes. Building trust, protecting your brand, and making sure that every can that comes off the line is something you can be proud of are the main goals. Aerosol producers are able to fulfill and even surpass expectations by putting strict standards into place, utilizing contemporary technologies, and concentrating on ongoing improvement.
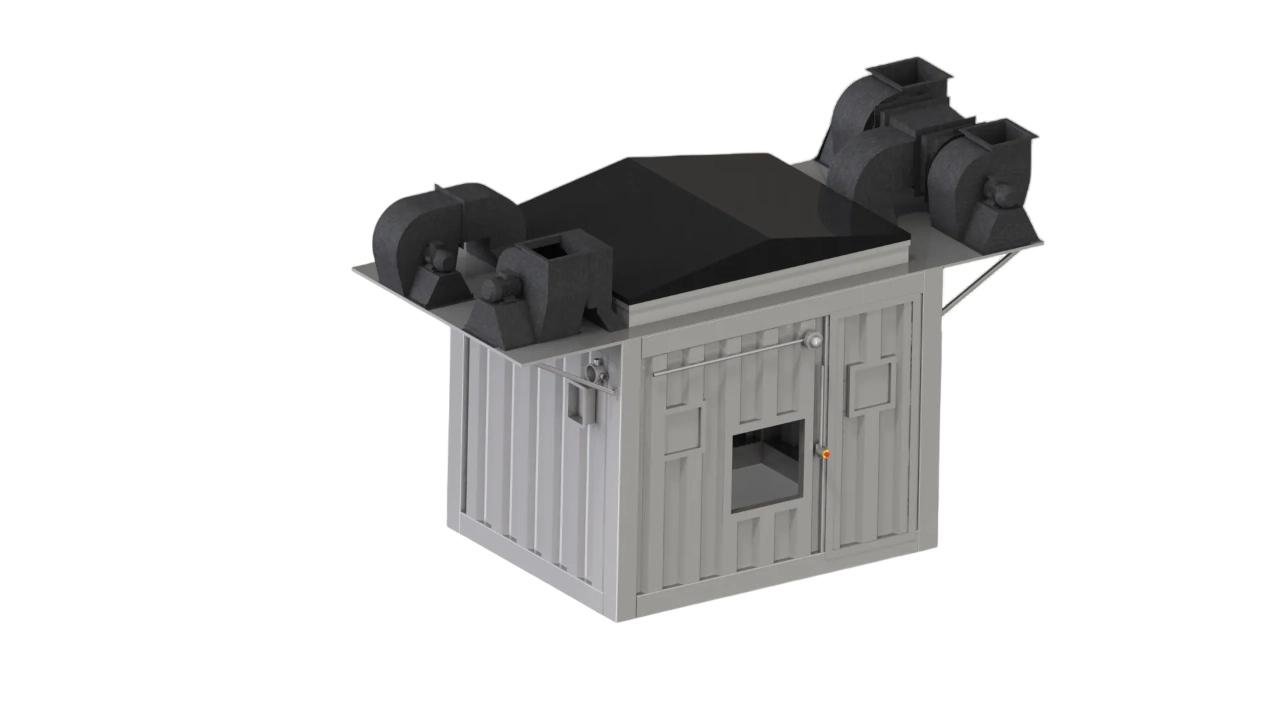