The complex relationship between product formulation and the filling process is more than just a technical need in the field of aerosol technology; it is a determining factor in the quality of aerosol production. The properties of the formulation have a direct impact on the performance of the filling machine and the entire production line, regardless of whether the product is a food-grade aerosol, pharmaceutical spray, or personal care item. Filling line tests make this link clear since even little formulation errors can affect leak control, spray performance, and valve crimping. In this article, we will delve into the key aspects of how formulation affects the production line and how industrial packaging is shaped by technological precision and regulatory standards.
Quality Control Processes in Aerosol Filling Lines: From Leak Tests to Weight Control
A strong quality control procedure is one of the most important foundations of an effective aerosol production process. Leak testing, a crucial step in ensuring that no product escapes from the container after filling, is the first step in contemporary filling lines. These tests typically involve water baths, pressure decay systems, or high-speed sensor-based equipment, which quickly detect imperfections.
Alongside leak testing, weight control plays a significant role. Here, automatic checkweighers continuously verify that the right amount of product has been filled. This step is greatly impacted by the viscosity, volatility, and pressure behavior of the formulation. For example, the behavior of a liquid and a foam-based formulation will differ, requiring various filling methods and speeds. Hence, the formulation isn’t just a product—it becomes a production variable.
In short, the tighter the tolerances in filling line tests, the better the production line can perform without stoppages. Additionally, these tests guarantee regulatory compliance and customer satisfaction, especially for goods in the food or pharmaceutical industries.
Aerosol Valve Crimping: Ensuring a Perfect Seal
Valve crimping is another area where formulation properties meet mechanical precision. The method used to crimp the valve onto the can must change depending on how the product behaves within. Excessive pressure applied by a formulation during or after filling may weaken the crimp and cause leaks or even dangerous explosions.
A proper crimp requires more than just machine calibration; it also requires knowledge of how the formulation and valve components interact. While excessively acidic or basic formulations may erode the valve housing, some propellants or solvents can break down the rubber gasket. During aerosol production quality testing, any such mismatch is flagged, ensuring that each can holds up through transportation and shelf life.
For this reason, formulation testing is often done hand-in-hand with valve compatibility checks. Crimp diameter, depth, and pressure must be calibrated not only for the valve model but also for the specific formulation characteristics.
Aerosol Packaging Materials: Comparison of Tinplate, Aluminum, and Glass Cans
Both formulation compatibility and filling line capability have a direct impact on the material selection for aerosol packaging. Each of the most popular can types— aluminum, and tinplate—has unique benefits and drawbacks.
Tinplate cans are renowned for being affordable and long-lasting. In contrast, aluminum cans are lighter and have superior corrosion resistance, both of which are beneficial for logistics. Additionally, their smooth structure improves both safety and aesthetics.
Long-term integrity and safety in industrial packaging are guaranteed by the compatibility of the product formulation and the can material. As a result, when working with flammable or reactive components, the material selection and filling line design must be coordinated.
Food Aerosols: Special Safety, Regulations, and Filling Requirements
Food aerosols add a level of complexity that goes beyond simple mechanical modifications; they necessitate rigorous adherence to legal requirements, such as those set forth by the FDA. The formulation needs to be sterile because food is consumed, and each stage of the filling line needs to guarantee cleanliness and contamination-free operation.
These lines often use cleanroom environments, stainless steel components, and specialized cleaning protocols. The formulation’s characteristics—such as viscosity, particulate size, or thermal sensitivity—require adapted filling speeds and temperature controls.
The filling line for food aerosols is not just a machine—it is a carefully engineered system where product characteristics affect the line from start to finish.
Energy Efficiency and Cost Reduction Opportunities for Aerosol Filling Lines
Energy consumption in aerosol filling lines is increasingly under scrutiny, especially as sustainability becomes a key driver in industrial production. Energy-efficient motors, servo-driven systems, and optimized air compression systems are now being implemented to cut down electricity and compressed air use—two major cost contributors in any aerosol plant.
Formulation viscosity and spray behavior also influence energy consumption. While volatile solvents may require improved ventilation or explosion-proof zones, thicker materials may require longer fill periods or pre-heating.
Manufacturers are also spending money on intelligent control systems that adjust in real time to variations in temperature, line pressure, or product viscosity in an effort to cut expenses. These solutions improve uptime and lessen the risk of downtime in addition to lowering operating costs.
Therefore, cost-efficiency is no longer just dependent on the filling machine; rather, it is the outcome of designing each step of the manufacturing line with the formulation in mind.
Safety Culture and Operator Training in Aerosol Lines
With aerosols, safety is paramount—not just from a consumer standpoint, but within the production environment as well. High-pressure containers, flammable propellants, and complex machinery mean that a strong safety culture is not optional—it’s essential.
Operator training is a critical component here. Personnel must understand not only how the filling machine works, but also how different formulations behave under pressure.
Aerosol Spray Performance: The Impact of Valve, Actuator, and Formulation
Lastly, spray performance—a feature that is greatly impacted by the collaboration of the valve, actuator, and formulation—determines the final user experience of an aerosol product. The formulation controls consistency and dispersion, the valve controls flow rate, and the actuator forms the spray pattern.
In this phase, filling line tests help validate spray pressure, particle size distribution, and discharge rate. If the formulation is too thick or too thin, it can affect the internal pressure, actuator response, and consumer satisfaction.
Formulation adjustments, therefore, must go hand-in-hand with mechanical calibration and testing of valves and actuators. Only when all three elements are harmonized can the aerosol product deliver the performance users expect.
The filling line and aerosol formulation have a complex and dynamic connection. The chemical and physical characteristics of the product have an impact on every part, including valves, packaging, safety procedures, and quality control systems. Manufacturers must remain flexible as aerosol technology develops further, constantly modifying their production lines and filling machines to satisfy evolving formulations, more stringent laws, and evolving consumer demands.
The aerosol business can attain not only regulatory compliance but also superior product performance and production efficiency by means of operator training, filling line optimization, and strategic formulation testing. In the end, the formulation isn’t just what’s inside the can—it’s what defines the entire process around it.
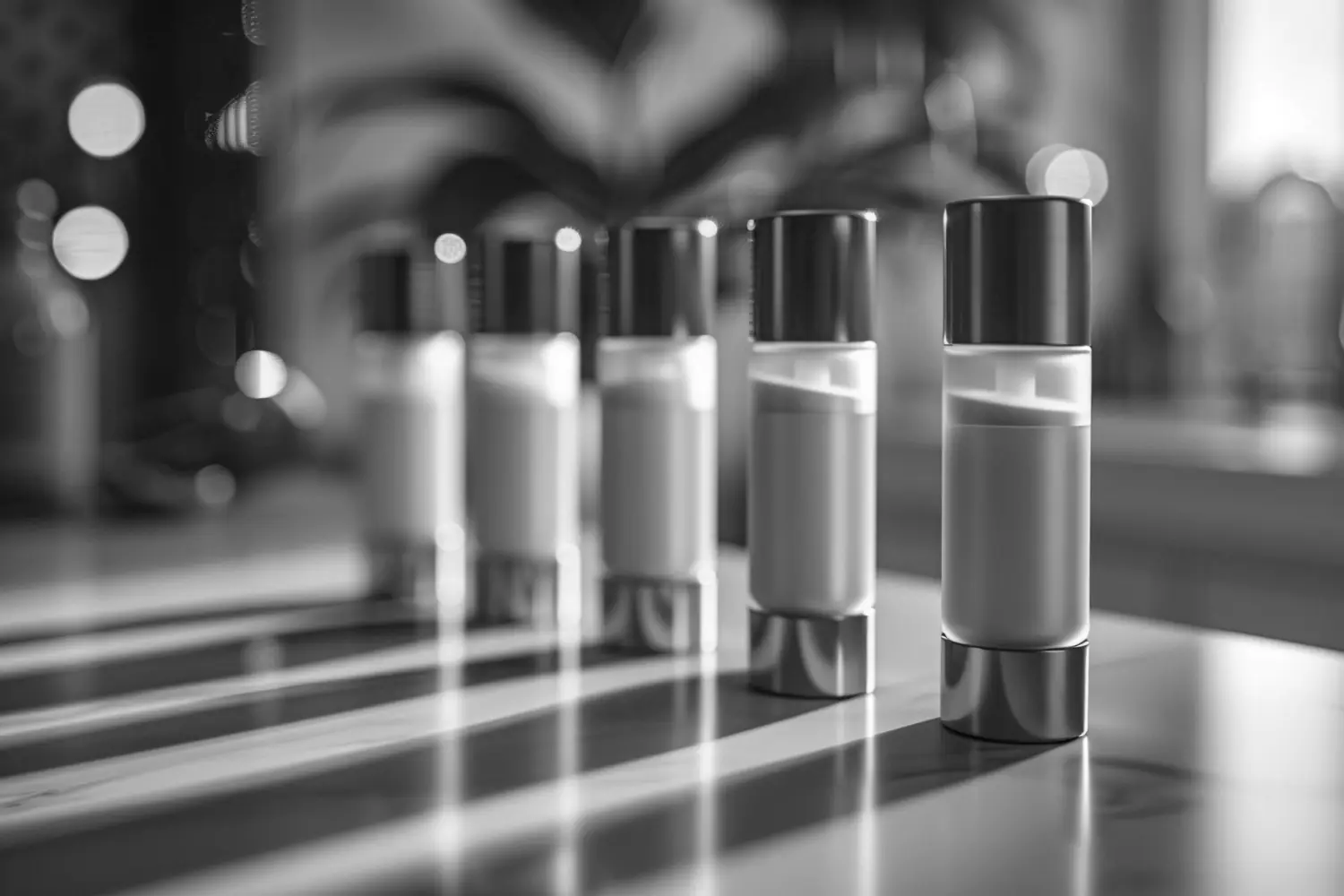