In the world of aerosol production, safety and compliance are from formulation to the delivery of the finished product, they serve as the foundation of the entire process. Examples of laws and safety requirements that have an impact on the creation, testing, labeling, and distribution of aerosol goods are provided. Because environmental concerns and consumer safety are becoming more and more important on a global scale, companies in the aerosol sector must adhere to national and international regulations in order to stay dependable and competitive.
This article examines the importance of stringent safety standards, the main rules, and how adherence to them contributes to the development of a better and more dependable aerosol production environment. We’ll also explore the potential future and how rules affect production operations. It is now essential for aerosol manufacturers to comprehend and incorporate compliance tactics; it is no longer an option.
Why are There Strict Regulations and Safety Standards in Aerosol Production?
The manufacture of aerosols has a legitimate reason for stringent safety restrictions. Hazardous materials including chemical components and flammable propellants are frequently found in aerosol goods, and they can be dangerous if not handled correctly. Serious injury may result from consumer misuse or industrial accidents. Because of this, governments and regulatory bodies have put solid frameworks in place.
Aerosol production isn’t just about filling cans. It’s about managing pressure, packaging, and volatile substances all at once. Safety standards help control every step—formulation, filling, labeling, and transport. There would be a far greater chance of workplace mishaps, defective products, and even explosions in the absence of these regulations.
Additionally, these standards aid in guaranteeing end users’ product safety. Consumers have faith that the goods on the shelf won’t hurt them or the environment. Strong adherence to industry standards and safety laws forms the basis of this trust. Because of this, safety in the production of aerosols is constantly a focus.
What are the Main Regulations and Standards Affecting Aerosol Production?
The production of aerosols is subject to numerous laws. The European Union’s Aerosol Dispensers Directive (ADD) is among the most significant. It addresses the fundamental safety standards for can integrity, labeling, and pressure. Before aerosol items are offered to customers, the directive makes sure they adhere to strict requirements.
The Importance of Complying with Regulations and Standards for Aerosol Manufacturers
Strict adherence to rules and guidelines is not only required by law but also essential to conducting business responsibly in the aerosol manufacturing sector. Products are guaranteed to be safe for customers, employees, and the environment when national and international safety, environmental, and quality standards are followed.
The health concerns connected to handling and using pressurized items are reduced when laws sucah as ISO standards are followed. Environmental regulations also seek to lower emissions, advance sustainability, and support the use of recyclable materials and environmentally friendly propellants.
Building trust with customers, business associates, and end users is another benefit of adhering to regulatory norms. It helps the business avoid expensive legal repercussions and product recalls, improves its reputation, and facilitates entry to global markets.
How Do Regulations and Standards Affect Aerosol Production Processes?
Every stage of the aerosol generation process is significantly impacted by regulations and safety standards. Manufacturers have to adhere to a precise plan from locating raw materials to final packaging. That roadmap ensures every component, every valve, and every label meets safety criteria.
Production lines need to be equipped with the right safety systems. Think fire suppression, pressure checks, and leak detection. Storage areas for flammable gases must meet certain ventilation and temperature control requirements. Even employee training must be aligned with regulatory expectations.
Let’s not forget documentation. A big part of compliance is keeping records—inspection logs, safety data sheets, and batch testing results. These records must be easily accessible in case of audits or incidents.
In terms of design, packaging is also impacted. For instance, containers must pass burst and drop tests to ensure they won’t fail under pressure. Labels must include warnings in the appropriate languages, as well as instructions and symbols that meet national and international standards.
Current Regulatory Changes and Future Expectations in the Sector
The regulations are changing along with the aerosol production industry. More sustainable packaging and propellants have gained popularity recently. Aerosol producers must so monitor changes to legislation that promote environmentally friendly innovation. More severe limitations on the use of dangerous products are anticipated in the future.
To put it briefly, the industry is moving toward production that is more accountable and transparent. For any aerosol company hoping to stay competitive and relevant, staying ahead of these changes will be essential.
Compliance Strategies for Aerosol Manufacturers
How can manufacturers, then, stay up to date? Creating effective compliance techniques is the solution. They must first establish a strong quality management system that addresses everything from post-market surveillance to procurement. Frequent internal and external audits assist in finding weaknesses before they become issues.
Employee training is yet another crucial tactic. The fundamentals of aerosol safety, labeling regulations, and handling hazardous materials should be understood by everyone, from engineers to warehouse employees. After all, it’s a team effort.
Collaborating closely with consultants or regulatory specialists can also have a significant impact. They can offer best practices suited to particular operations and assist in interpreting complicated regulations.
Lastly, audits and inspections go considerably more smoothly when compliance documentation is kept in a digital format. Software tools can be used to update SDSs, maintain certifications, and notify teams of impending regulatory changes.
Ultimately, compliance is about doing things correctly, not just about being safe. For producers of aerosols, it serves as a road map for increased quality, heightened consumer confidence, and sustained prosperity in a very competitive industry.
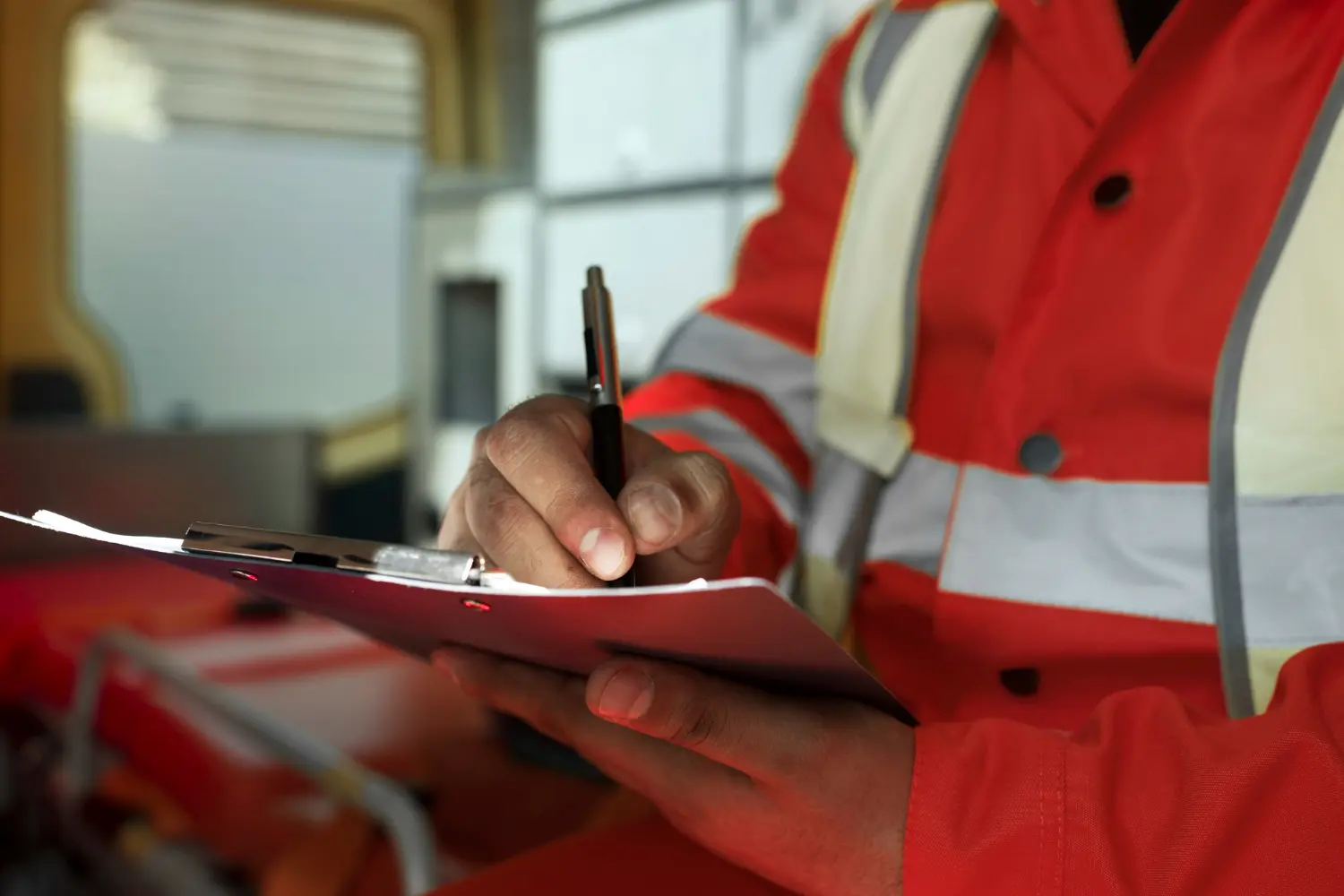